This website uses cookies so that we can provide you with the best user experience possible. Cookie information is stored in your browser and performs functions such as recognising you when you return to our website and helping our team to understand which sections of the website you find most interesting and useful.
Sustainability
The EU has considered Mboca as a highly dangerous carcinogen in its handling process (more information). And it has legislated the prohibition of the use of Mboca in the very short term [COMMISSION REGULATION (EU) No 895/2014, SUNSET DATE 22.NOV.2017 + EXTENSION 4 YEARS]
This is a problem because, although there are other dressings and in some applications the use of Mboca is not necessary (typical example: in the No Crush or Introducer Wheels), when the requirement of support for cutting and abrasion is combined, the new dressings developed until now they had not reached the level of performance offered by the MBOCA.
For this reason, with a strong R&D drive, anticipating legislative change and under the precautionary principle, a few years ago, we began the development of a new formulation with a different curative than Mboca. It is a new amine with a better toxicological profile and whose physical properties, after many series of tests on our own testing machine at Rodicut and subsequently in controlled tests on clients, have been perfected to obtain optimum application performance in die-cutting machines. Rotary. Very possibly, they have already used this new formula in some of the parts that we may have supplied them in recent months.
TODAY we announce it and launch MBOCA FREE®, the only Anvil Covers brand with a new dressing free of toxicological effects and guaranteeing the same, or even better, performance. And you will recognize this brand on the labels of our products.
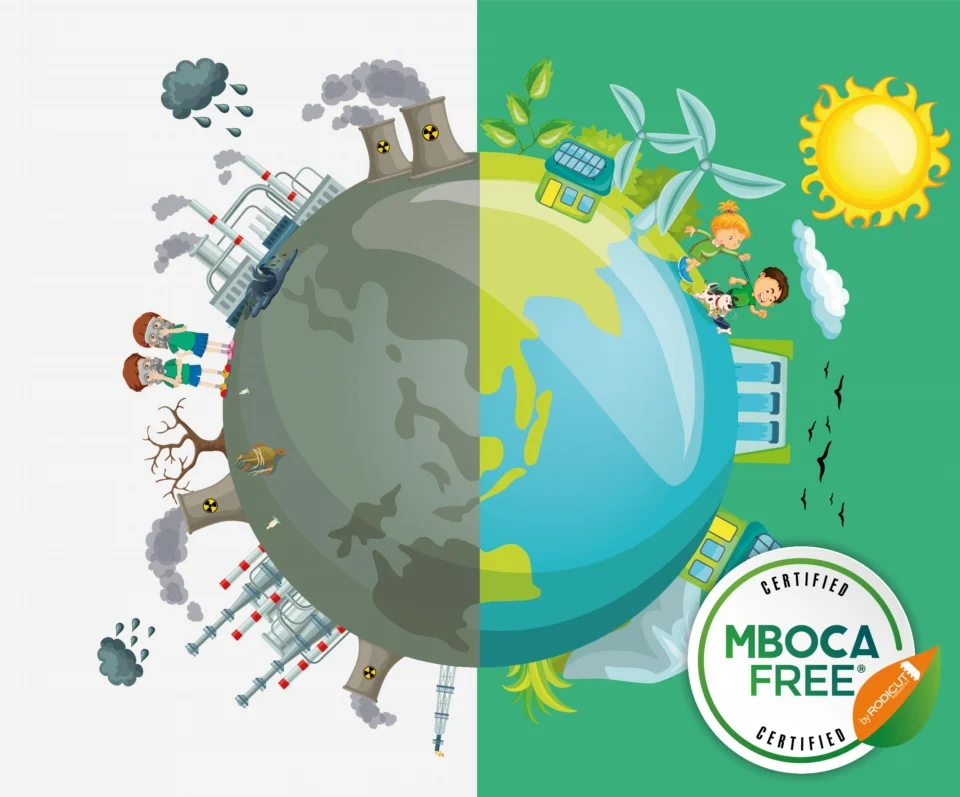
It is a synthetic material, with elastic capacity and with a strong internal structure that results in excellent mechanical properties.
This is due to the shape of its molecule, which combines resistance and elasticity in the same polymer (polymer = repetition of groups of molecules).
PURs contain urethane groups in their molecular structure. The chemistry is very varied depending on the isocyanate and the polyol used, hence materials with very different properties are attained. Commonly, the base are prepolymers that are mixed in the right proportion and react in presence of a catalyst to achieve the finished PU, in its final form.
Polyurethane success is based on its versatility. Rigid, flexible, foam, adhesive (coating)… it is the material of choice for a variety of applications. In one way or another, we use polyurethanes on a daily basis: at home, in the office, in our cars, in our sports and leisure activities… In the industrial area, polyurethane is present in a multitude of applications, and concerning compact polyurethane, it is especially indicated in applications where elasticity, resistance to cutting, friction and abrasion are required. This is particularly true in our flagship product, covers-counterpieces for rotary die cutting machines.
We manufacture compact polyurethane by casting in an open mold and through mixing a prepolymer and a curative agent. The reaction takes place during the boiling of the mixture. The high curing temperatures (up to 100 °C) generate a three-dimensional structure due to the cross-linking of the polymer chains, resulting in a thermostable plastic.
It is a synthetic chemical substance used as a curative agent in conjunction with the prepolymer for the production of polyurethane parts. Technically it is an excellent additive at a very competitive price. That’s why it has been widely used.
Mboca has toxicity levels and includes health risks that make it considered highly dangerous in production, so its storage and handling are carried out under strict safety measures to protect the health of exposed operators and the environment.
The EU has considered Mboca a highly dangerous carcinogen in its handling process (more info). And it has legislated the prohibition of the use of Mboca since November / 2021 [COMMISSION REGULATION (EU) No 895/2014, SUNSET DATE 22.NOV.2017 + EXTENSION 4 YEARS]
Yes, there are other curatives and in some applications the use of Mboca is not necessary (typical example: in the No Crush or Feeder Wheels). However, when cutting and abrasion resistance requirements are combined, the new developped curatives so far had not reached the level of performance offered by the MBOCA.
With a strong R&D drive, anticipating legislative change and under the precautionary principle, a few years ago we began the development of a new formulation with an alternative curative to MBOCA. It’s a new amine with a better toxicological profile and whose physical properties, after many series of tests on our own testing machine at Rodicut and later in controlled tests on customer sites, have been polished for optimum application performance on rotary die cutting machines. It’s quite possible you have already used this new formula in some of the parts that we could have supplied you in last months.
Since we are very satisfied with this achievement, TODAY we announce and launch MBOCA FREE®, the only brand of Anvil Covers with a new curative free of toxicological effects and guaranteeing the same, or even better, performance. You will recognize this brand within the labels of our products.
Without a doubt, it has been tested and approved! Since the beginning of 2019, RODICUT has carried out Mboca-free productions linked to the client’s wishes, with the aim of progressively increasing the % of free parts of this component and in parallel our consumption of the alternative amine.
Now available, do not hesitate to ask our usual commercial contact for information
Download product sheet.